Email Magazine
nitto
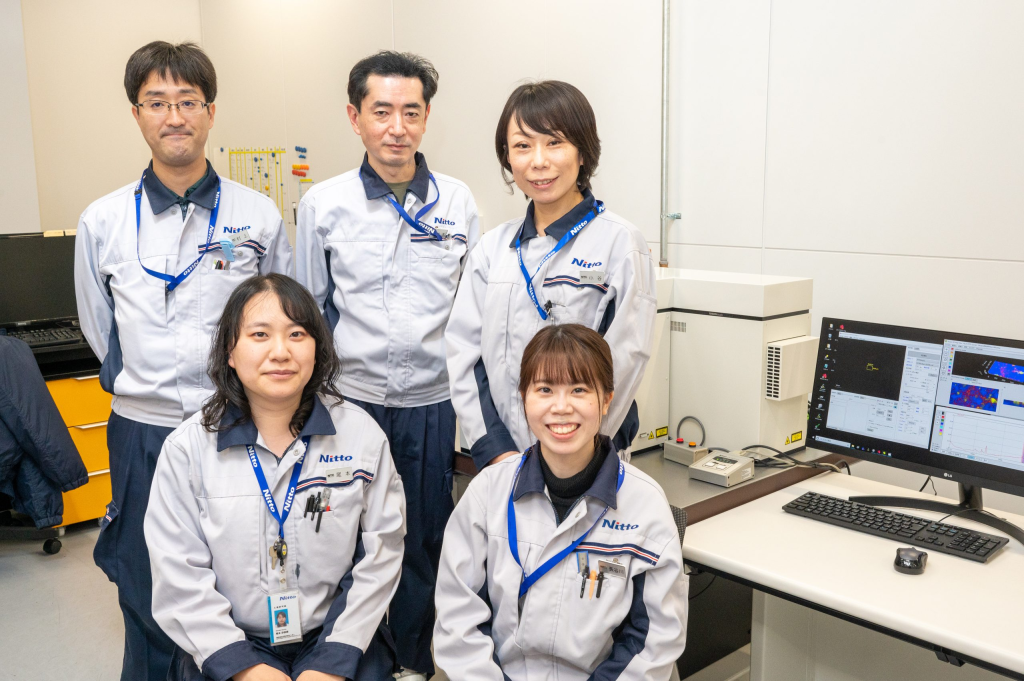
Nitto Analytical Techno-Center, an analysis company of the Nitto Group, introduced Nanophoton’s RAMANtouch in December 2020 and is using it effectively. I visited the company’s Ibaraki Analysis Technology Department (Ibaraki City, Osaka Prefecture) to hear about its activities. (Editor-in-Chief of the Email magazine / Science Writer Takeshi Nemoto)
The head office of Nitto Analytical Techno-Center is conveniently located an eight-minute walk from the station. We were greeted by members of the Surface Property Evaluation Group 2 of the Ibaraki Analysis Technology Department. First, they showed me the room where RAMANtouch is installed.


Moving to the conference room, I heard explanations from Shuichi Murakami, Team Leader of Team 2, Rie Kotani, Chief Technologist, and Kana Hasegawa, Deputy Chief Technologist. Ms. Kotani and Ms. Hasegawa are in charge of Raman microscopy, and they use RAMANtouch on a daily basis.

– – – First, please introduce Nitto Analytical Techno-Center.
Mr. Murakami: Nitto Analytical Techno-Center is one of the Nitto (Nitto Denko Corporation) group companies. 99 Nitto group companies (as of January 2023) are located in Japan and overseas, employing a total of 28,000 people. As of FY2021, the overseas sales ratio will reach 80%.
It manufactures a wide variety of products, including polarizing plates and adhesive tapes for smartphones and computers, filtration membranes to clean water, and plastic optical fibers. Most of its products are BtoB, but BtoC is also available. “Korokoro (sticky roller),” an adhesive cleaner that removes debris from floors and other surfaces, is a registered trademark of Nitto Group company Nitoms.
– – – I use Korokoro a lot!
Mr. Murakami: Nitto Analysis Center was established in 1974 when members of the analytical field were spun off from the technical research laboratory of Nitto Denki Kogyo K.K. (now Nitto). Analysis bases are located here at the head office in Ibaraki City, Osaka Prefecture, and in Toyohashi City, Aichi Prefecture, and Kameyama City, Mie Prefecture, all co-located on the same site where Nitto’s plant is located. Sales offices include the Osaka Sales Office and the Chubu Sales Office in Toyohashi, as well as the Tokyo Sales Office.
The company has 173 employees (as of April 2022). The sales ratio is 70% analysis commissioned by the Nitto Group, with the remaining 30% coming from outside sources to measure a variety of samples.

– – – There are many analysis centers in the world. What makes Nitto Analytical Center strong?
Mr. Murakami: The parent companies of other analysis companies are often materials manufacturers and are independent from them, giving them an image of being strong in composition analysis of raw materials. On the other hand, Nitto, our parent company, is an intermediate materials manufacturer, so it purchases raw materials and develops processing technologies to add functions to them, such as drawing, sputtering, and composite use of materials to create new functions. In doing so, we use analysis to evaluate the structure of the material in its functional state, and sometimes we also develop new technologies. For this reason, we believe that our analytical technology is strong in “polymer analysis technology for clarifying the mechanism of function expression.
Mr. Murakami: Furthermore, we are looking to develop and expand upon these strengths. For example, if we have a process that pulls a material, we want to evaluate it in the state of pulling. If a material becomes hard when heated, we want to see how it changes in real time while being heated. Furthermore, there are many things we want to see, such as the state of the bonded interface, composition and morphology changes under humidity-controlled and temperature-controlled conditions, and how molecules line up as a result of stretching. For this reason, we are aiming for dynamic, in-situ, 3D measurements.
– – – What is dynamic, in-situ, 3D measurement?
Mr. Murakami: When explaining dynamic, in-situ, 3D measurements, I often bring up the picture of a squid. To understand the function of a squid swimming, you need to examine it as it is in its swimming state. Conventional analysis cannot be done while the squid is alive, and measurements are made almost exclusively in the dried, surume state or, if possible, in the sashimi state. That is a static assessment. Instead, it is still better to see them in the sea to understand their functions, so we are trying to create a technology to measure squid swimmingly as a strength.

– – – Has Nanophoton’s Raman microscope been helpful in achieving this goal?
Mr. Murakami: Yes, we have. We are not yet at the point where we can evaluate the state of the squid swimming, but to get as close as possible, we installed a Nanophoton device that can make high-speed measurements. We needed it to capture the ever-changing conditions at high speed, because the RAMANtouch has a mechanism called “line illumination,” which obtains data from 400 points in a straight line at once. This means that we bought this mechanism.
Ms. Kotani: When selecting an instrument, we brought the same sample to various instrument manufacturers for measurement, and the RAMANtouch was the fastest in terms of speed.
Mr. Murakami: This is one of the strengths of the Raman microscope, but it is also helpful to be able to place a sample under the microscope and measure it. With other analyzers, there may be restrictions such as the need for a vacuum system. With dynamic, in-situ, 3D measurement, we can measure by placing heating and humidifying devices and stretching jigs under the microscope. Of course, high resolution is also an advantage.

Ms. Kotani: With conventional equipment, we had to think about various things, such as how to put the device into the equipment and devise measurement conditions, in order to control the environment, such as temperature and humidity, and conduct dynamic evaluations. With RAMANtouch, however, as long as the device can be inserted into the equipment, the rest can be cleared by using various on-board functions and considering the measurement conditions. The fusion of RAMANtouch and the various pre-processing and analysis technologies we have cultivated has made it possible for us to do many things that were not possible before.
– – – Besides high speed measurement, are there any other reasons for your choice?
Mr. Murakami: Imaging. Raman measurements produce spectral data, but it is difficult to convey this data to customers by showing them spectra. Rather than saying, “This peak is higher,” it is better to show an image and say, “This is how it has changed.


Ms. Kotani: Imaging images are easy for anyone to understand and have an overwhelmingly strong impact. We often evaluate the distribution of components that express the function of optical and adhesive materials, and imaging images are very important. We try to provide our customers with data in the form of imaging images rather than spectra. For example, by showing that “the distribution changes in this way after a few minutes,” the customer can clearly understand the content at a glance even if he or she cannot read the spectrum.
– – – Please provide examples of dynamic, in-situ, 3D measurements.
Ms. Hasegawa: We present a three-dimensional compositional distribution analysis of hand cream. Compositional information on how mineral oil, water, and paraffin are distributed in three dimensions can be obtained from cross sections in various directions on a PC monitor.
In the video, you can see how the mineral oil is reticulated and water is held within it. Paraffin is also localized in the area of the mineral oil. Since this cannot be seen in 2D, I think this technology can contribute to better product design for our customers.


– – – Can Nitto Analytical Center perform this 3D component distribution analysis?
Ms. Hasegawa: Yes, we have it on our website (https://www.natc.co.jp/result/r2280922/). You can also watch the video (https://www.natc.co.jp/movie/movie18/).
We took dozens of 2D images in the X-Y direction, shifting them slightly in the depth direction, and superimposed them to create a 3D image. To create the movies, we used not only Nanophoton’s analysis software but also another software.
– – – This is easy to understand.
Ms. Hasegawa: Since hand cream dries out over time, the ability to measure at high speed helps to obtain a 3D image. This measurement could be completed in 30 minutes.
– – – Are there other examples of measurements?
Ms. Hasegawa: We plan to post on our website an example of a PET film being measured while being pulled from both sides. 1 minute intervals were measured, and when connected together to make a movie, the changes in stress, crystallinity, and orientation during the pulling can be seen.

Ms. Kotani: The ability to measure such a large range in one minute is the wonderful thing about line illumination. It would be difficult to evaluate the same resolution and measurement time with ordinary point measurements.
Ms. Hasegawa: Combining high-speed imaging capabilities with stretching and humidified heat fixtures, various dynamic in-situ evaluations can now be performed.

– – – How easy is RAMANtouch to use?
Ms. Hasegawa: First, operation is intuitive and easy to understand. All operations, such as raising and lowering the stage, switching the objective lens, and turning the laser on and off, can be performed using a PC and mouse. Even when new employees come for training, they quickly learn how to use the system, reducing the time allotted for training.
Ms. Kotani: The stages were all motorized (at a cost), which was great because it made them easier to work with. It was useful when I was unable to come to work due to the corona virus pandemic and had to take measurements from home. Someone just has to put the sample on the stage, and the rest of the data can be taken remotely.
Ms. Hasegawa: It is also convenient that the stage rotates. This is essential when evaluating the state of ……, where the molecular structure is oriented in this direction after stretching.
– – – What are your expectations for Nanophoton in the future?
Mr. Murakami: As an Osaka University start-up company, I can really feel the desire to “create something good with Raman.” Actually, we had considered introducing Raman lighting around 2011, before we introduced it in 2020. At that time, I was not satisfied with some aspects of Raman lighting and decided against it, but by the time of 2020, improvements had been made. So I am looking forward to seeing what devices and functions they will develop in the future. I would like to see not only the speed of measurement, but also the ability to see smaller objects. Nanophoton is planning to increase the number of employees, so I have high expectations.